Precautions For Plate Making Before Printing Of Color Box
29-01-2020
Precautions For Plate Making Before Printing Of Color Box
corrugated mailer boxes
In the process of packaging color box printing, quality problems often occur due to inadequate pre-press platemaking. Light materials and man-hours are wasted, and products are scrapped in serious cases, causing serious economic losses. In order to prevent the above problems, the editor of Lijia thinks that the following aspects should be paid attention to.
recyclable paper box
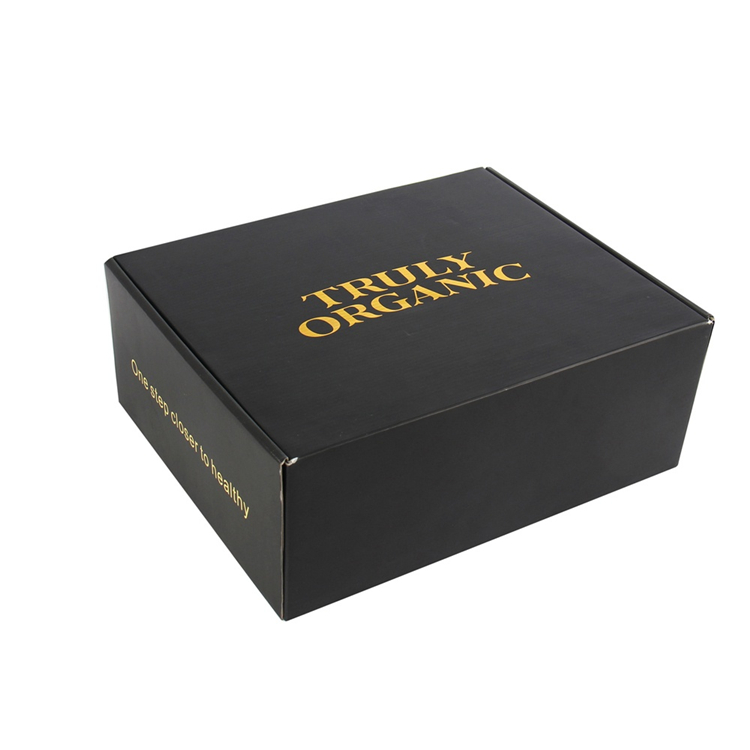
(1) When different types of color boxes need to be spelled on a printing plate for printing, if products with the same or similar hue are not spelled in the same vertical position during the imposition, it may appear that A products can meet the proofing standards, B This product is basically close to the proof standard. The C product has a slight color difference from the proof, and the D product has a large color difference from the proof. Therefore, the warm, cold and mid-tone products should be spelled in the same vertical position during the imposition in order to print high-quality products.
foldable paper box
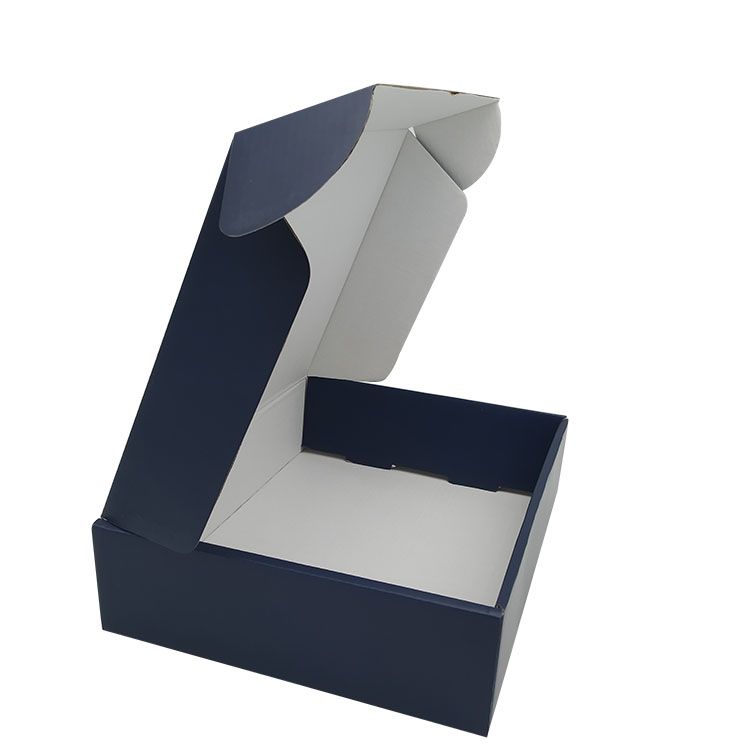
(2) If the non-graphics part of the color box is placed at the mouth when the imposition, and the continuous drag image is not placed on the trailing edge, it is a flat screen or the field, then it is easy to produce "ghost shadows" when printing. Seriously affect product quality. At this time, the non-graphic parts should be placed on the trailing edge, so that "ghost shadows" will not appear.
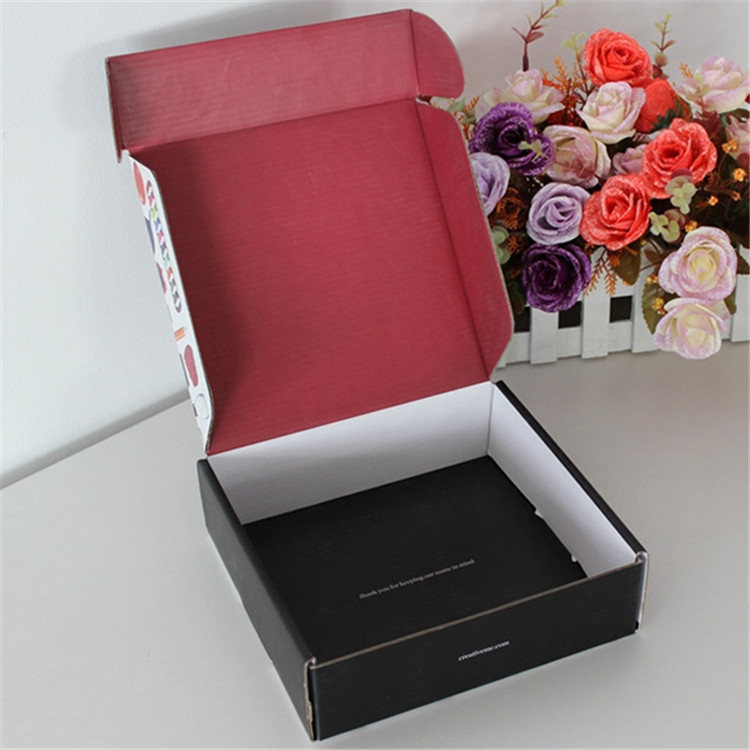
(3) At the time of imposition, you should also pay attention that you cannot save the finished product line of color boxes in order to save film, but rely on the printing and printing staff to calculate the position of the mouth and the finished product. This will greatly affect the production efficiency, and may also Negligence with the printing staff caused a serious accident.
Packing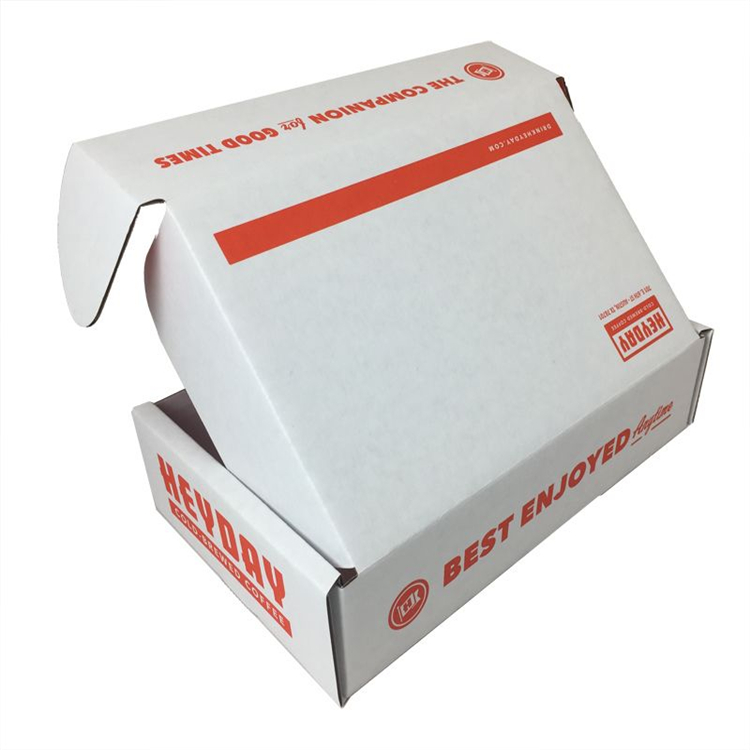
box
(4) The output film usually does not contain the pull gauge identification line, but if the gap and the trailing edge are blank, it will bring great inconvenience to the printing and positioning of the color box. For this reason, it is necessary to make a pull gauge marking line on the film. For packaging color boxes that do not require corrugated cardboard, the pull gauge identification line is made at the body part; for packaging color boxes that require corrugated cardboard, the pull gauge identification line is made outwardly.
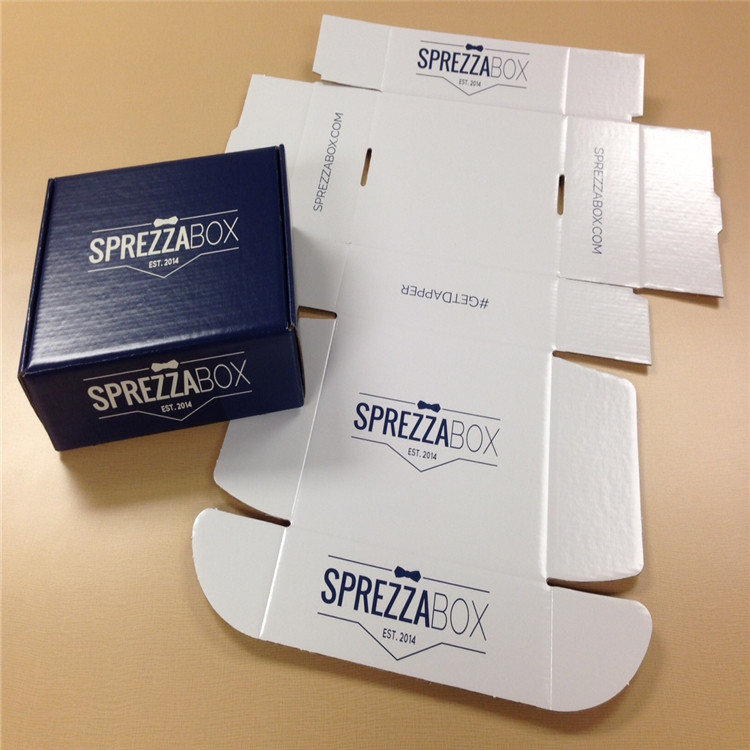
(5) Make sure that the film meets the printing requirements. After the film is output, carefully check whether the graphics on the film are consistent with the proof (the color line of the color box used as the benchmark for verification must be standardized).
paper box printing 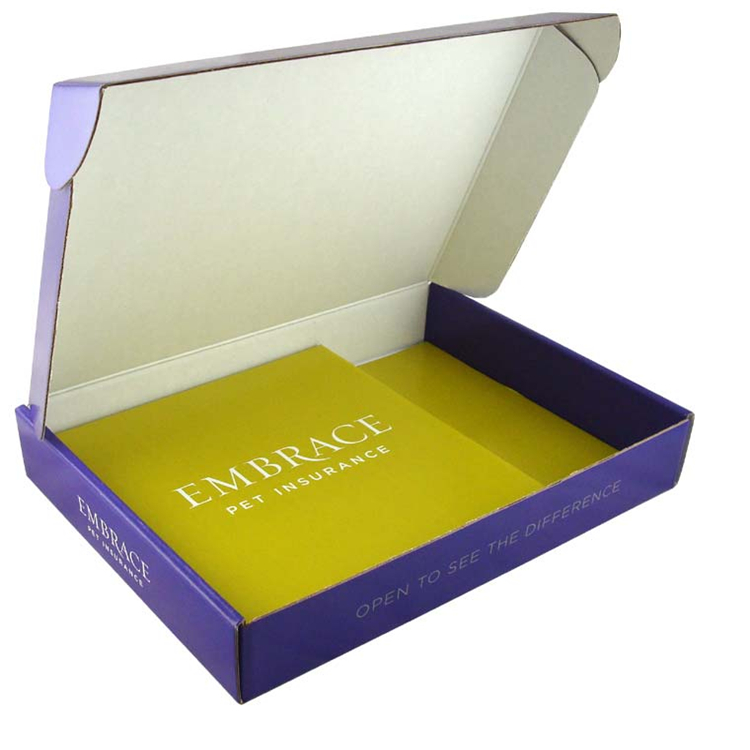
(6) To ensure the correct registration between different films. This is because a set of films is usually output in two times, and its overprint accuracy is easily affected by some objective factors. Once the output film has quality problems, it should be remade.
toy paper box 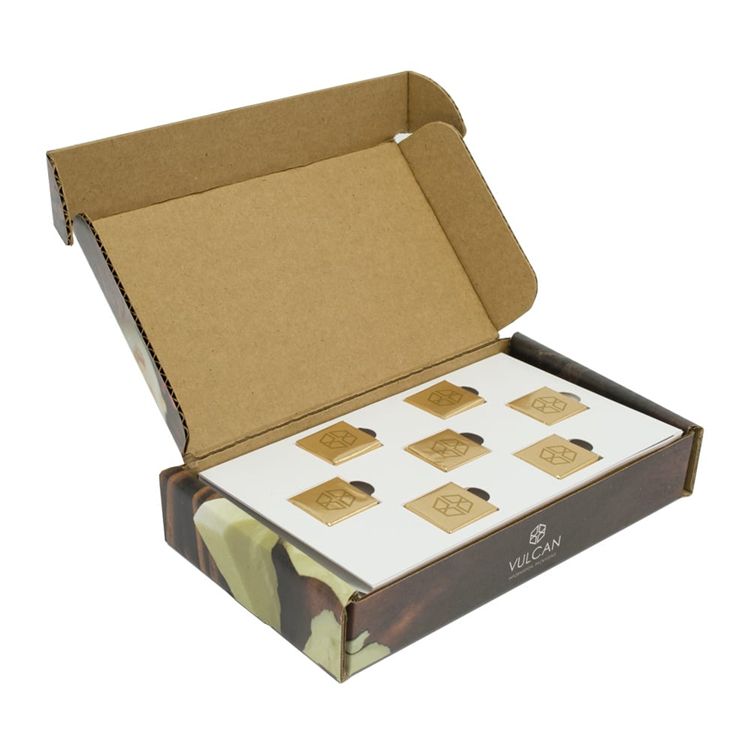
(7) The film and proof should be carefully compared before printing. If the film density of the main color is too high, the exposure time during printing should be increased to avoid the printing tone being too heavy. If the density is too small, the printing time should be reduced. Exposure time to prevent dot loss from affecting color reproduction.
Get the latest price? We'll respond as soon as possible(within 12 hours)